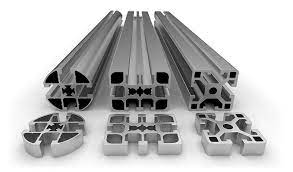
Introduction
Aluminum extrusions is a highly versatile manufacturing process that involves shaping aluminum alloys into specific profiles with consistent cross-sections. This process offers numerous benefits that have made it a preferred choice in various industries, including construction, automotive, aerospace, electronics, and more. In this article, we will delve into the advantages of aluminum extrusions, highlighting their wide-ranging applications and the reasons behind their popularity.
Lightweight and Strength
One of the key advantages of aluminum extrusions is their exceptional strength-to-weight ratio. Aluminum is a lightweight material, weighing approximately one-third of steel. However, it possesses remarkable strength properties that allow it to withstand heavy loads and stresses. This unique combination makes aluminum extrusions an ideal choice for applications where weight reduction is crucial, such as in the aerospace and automotive industries. By utilizing aluminum extrusions, manufacturers can achieve significant weight savings without compromising structural integrity.
Flexibility in Design
Aluminum extrusions offer immense design flexibility, enabling the creation of complex shapes and intricate profiles. The extrusion process allows for precise control over dimensions, tolerances, and surface finishes, providing manufacturers with the ability to tailor the product to their specific requirements. This versatility opens up a multitude of possibilities, allowing designers to incorporate features such as grooves, holes, flanges, and internal chambers directly into the extruded profiles. As a result, aluminum extrusions can be seamlessly integrated into various applications, ranging from architectural structures to electronic enclosures.
Cost Efficiency
Aluminum extrusions provide significant cost advantages over alternative manufacturing methods. The extrusion process is highly efficient, allowing for high-volume production with minimal material waste. The ability to extrude long lengths of profiles also reduces the need for additional joining or welding processes, leading to further cost savings. Moreover, aluminum is a readily available and recyclable material, making it cost-effective and environmentally friendly. The durability and corrosion resistance of aluminum extrusions contributes to their long service life, reducing maintenance and replacement costs in the long run.
Corrosion Resistance
Aluminum possesses a natural oxide layer that forms upon exposure to air, providing inherent corrosion resistance. This oxide layer acts as a protective barrier, preventing the metal from reacting with the environment and offering excellent durability even in harsh conditions. Additionally, aluminum extrusions can be further enhanced with surface treatments, such as anodizing or powder coating, to improve their resistance to corrosion, UV radiation, and wear. This corrosion resistance makes aluminum extrusions suitable for outdoor applications, marine environments, and areas with high humidity.
Thermal Conductivity
Another notable benefit of aluminum extrusions is their high thermal conductivity. Aluminum efficiently conducts heat, allowing for effective heat dissipation and thermal management. This property is particularly advantageous in applications where temperature control is crucial, such as heat sinks for electronic components or cooling systems for industrial processes. The ability of aluminum extrusions to transfer heat efficiently helps prevent overheating and ensures optimal performance and longevity of the products.
Sustainability and Recyclability
In today’s environmentally conscious world, sustainability is a critical consideration. Aluminum extrusions align well with sustainable practices due to their recyclability and energy efficiency. Aluminum is 100% recyclable without losing its inherent properties, making it a highly sustainable material choice. The energy required for recycling aluminum is significantly lower compared to primary production, resulting in reduced carbon emissions. Choosing aluminum extrusions promotes resource conservation, waste reduction, and a greener approach to manufacturing.
Electrical Conductivity
Aluminum is an excellent conductor of electricity, making it an ideal material for electrical applications. Aluminum extrusions can be used in the production of conductive busbars, heat sinks, and electrical enclosures. The high electrical conductivity of aluminum ensures efficient transmission of electrical currents, minimizing power losses and optimizing system performance. This characteristic is particularly valuable in industries such as power distribution, renewable energy, and electronics.
Machinability
Aluminum extrusions offer excellent machinability, making them easy to cut, drill, mill, and machine into precise shapes and sizes. This property allows for efficient manufacturing processes and reduces production time. The machinability of aluminum extrusions also facilitates the incorporation of additional features or modifications as per the specific requirements of the application. Manufacturers can easily create intricate designs and assemble extruded profiles with other components, simplifying the overall production process.
Aesthetics and Finishing Options
Aluminum extrusions can enhance the visual appeal of products due to their aesthetic qualities and a wide range of finishing options. The extruded profiles can be anodized to provide a durable and attractive surface finish in various colors. Anodizing not only enhances the corrosion resistance of aluminum but also allows for customization and branding. Additionally, aluminum extrusions can be powder coated or painted to match specific design requirements and create a cohesive appearance when used in architectural applications or consumer goods.
Sound and Vibration Dampening
Aluminum extrusions exhibit excellent sound and vibration-damping properties. They can be effectively used to reduce noise and vibration in applications such as enclosures, automotive components, and industrial machinery. The inherent damping characteristics of aluminum help absorb and dissipate vibrations, thereby minimizing noise levels and enhancing the comfort and performance of the end product.
Fire Resistance
Aluminum is a non-combustible material, and aluminum extrusions offer inherent fire resistance. They do not contribute to the spread of flames, making them suitable for applications that require compliance with fire safety regulations. In situations where fire resistance is crucial, such as building facades, transportation vehicles, or electrical enclosures, aluminum extrusions provide an added layer of protection.
Non-Magnetic Properties
Aluminum extrusions are non-magnetic, which can be advantageous in certain applications. Industries such as electronics, telecommunications, and medical devices often require non-magnetic materials to avoid interference with sensitive equipment or magnetic fields. Aluminum extrusions offer a viable solution by providing structural support or housing while eliminating the risk of magnetic interference.
Conclusion
Aluminum extrusions offer a plethora of benefits that make them highly desirable across various industries. Their lightweight, strong, and flexible nature, combined with cost efficiency, corrosion resistance, and thermal conductivity, makes them suitable for a wide range of applications. Moreover, their sustainability, recyclability, and ease of machining contribute to their appeal. Whether it’s in the construction, automotive, electronics, or aerospace sectors, aluminum extrusions continue to prove their worth as versatile and advantageous manufacturing solutions.